news
Colour Design Pt. 5: Finalizing the Colour Module Format November 14, 2013 13:55 3 Comments
Demonstrating how Colour works for the upcoming Kickstarter video. Photo by Zach Robbin.
Colour as a Platform
There are four parts to a complete Colour unit: the Palette (motherboard) and three Colours (modules). The palette provides all of the power, I/O, control, and gain/attenuation circuitry to the colours, which provide the, well, color. (As an American, I spell 'color' with five letters. Co-designer Link Simpson is Canadian, hence the 'u'.) And while we're releasing three colours of our own with the palette, Colour is intended to be first and foremost a platform for the community to experiment with analog saturation circuits. Therefore, defining the specifics of the modular format was one of the most important and labored-over design decisions in the project. My design goals were for the colours to:- have as much vertical clearance as possible for large components;
- make a solid mechanical connection with the palette;
- make a solid electrical connection with the palette;
- mount/dismount quickly and easily;
- be protected against being inserted backwards.
To address the first concern, I opted for 1/8" standoffs, so that the mounting surface for components on the colours was only 3/16" higher than the palette. This leaves .968" of clearance for colour components within the allowed 1.5" 500-series space, enough room for large caps and small transformers.
When I turned to choosing standoffs, I realized that design goals 2 and 3 stand in opposition to each other: in most cases, the sturdier the connector, the more time and work it takes to fasten and unfasten. After ordering and demoing several different snap- and screw-in standoffs, the one I found that married sturdiness and convenience most happily was the Keystone 9018 (pictured). The 9018 spacers allow the colours to be simply pressed in, instead of screwed, and the locking nylon tabs ensure the colour cannot be removed without squeezing the tabs together.
Electrical Connectors
Finding the perfect electronic connector involved negotiating between another set of contradictory design goals: 1 and 3. By reducing the space between the colours and the palette to make room for big components on top of the colours, I had given away the space I needed below for the .100" pins and headers I had previously chosen for the electrical connectors. My first attempt at a solution was to remove the connectors altogether and place pads on the PCBs of the palette and colours themselves that would mate when the colours were screwed down. This would eliminate the need for spacers as well, since the colours could mount on the same standoffs as the palette PCB. And it would buy an extra 1/8" of clearance for the colour components!
The ill fated spacer- and connector-less colour mounting approach.[/caption] Unfortunately, it proved impracticable for a couple of reasons. First, it required large regions of the palette PCB to be routed out to provide clearance for the bottom of the colour PCBs. This compromised the structural integrity of the palette board and made wiring and grounding more risky. Second, the PCB pads simply did not mate very well. The connections between some pads were intermittent, depending on how thick the plating was on adjacent pads. So it was back to the now-familiar process of catalog digging, sample ordering, evaluating, and repeating. Except this time the process was almost a pleasure, since it turns out there is a company called Samtec kicking the connector industry's ass from here to next Tuesday. Samtec is the only electronics manufacturer or distributor I've come across with a truly functional, 21st-century website that makes it easy to find, sample, and buy their components. And they happen to make a .100" header sits on top of the PCB and mates with pins from below. Brilliant! Problem solved. (Note to other US/European manufacturers: give me a functioning website, phone support, and free samples and I will give you my money!)
The final colour mounting solution, with Keystone spacers and Samtec .100" connectors.[/caption] Finally, to meet design goal 5, I've offset the front row of electrical connectors so that the colours can only be inserted into the palette in one direction. This protects the colours from being destroyed by plugging the audio inputs into the power output connectors. This small revision will be implemented in the final PCB.
Making Your Own Colour
If you're interested in developing your own colour, or just playing around with the format, bookmark the Colour Module Design Guide. The design guide will host PCB templates and self-etch files, and pre-made colour proto-boards will be available soon. Thanks, as always, for following along and please do stay tuned for the next post in which I'll discuss the kit ordering options and, of course, the price!Coming Soon: Micro "Circuit Building Block" Kits August 23, 2013 13:39 8 Comments
The first two off the bench are balanced input and output boards. Both boards are based around THAT Corp's state-of-the-art integrated circuits (but also pin compatible with offerings from TI and Analog Devices) and include noise filtering, DC-offset protection, and power supply bypassing. At a tiny 1.4" x 1" (25 x 36mm), the boards are also intended to be small enough to retrofit into your consumer-level, unbalanced gear.
Balanced Line Driver PCB[/caption] Once I have received and tested the boards, PCBs and parts kits will be available from the store. Full kits for each will be around $20.
Colour Design Pt. 4: Big Time Interface and Circuit Overhaul August 9, 2013 17:40 16 Comments
In summary, after doing some mixes with the most recent prototype pictured below, I became dissatisfied with the current approach of feeding the dry signal to the colours in parallel and controlling how much of each is mixed in with the dry signal. I found that in almost every application, I was keeping the colours cranked all the way up and turning the dry signal all the way down. In retrospect, this makes sense, as the colours themselves are tuned to impart only subtle distortion, the way a colored preamp or compressor might.
The most recent physical prototype (#4) with JFET, tape, and Cinemag colours installed.[/caption] So I went back to the drawing board, this time with some real mixing experience in hand. One of the first things I knew I wanted to do was simplify the interface. While the idea of having control over the amount of each colour is tempting on paper, in practice I found that I didn't want to be bothered. What I did find myself doing was turning individual colours up and down quickly to hear what the signal sounded like with them bypassed. So I decided to substitute the individual colour volume controls for simple in/out switches. This interface trades a little control for a lot of ease and simplicity. This jives with my original intuitions about Colour: that, like a preamp or tape machine, a harmonics generator is not a piece of gear people want to spend significant time tweaking. Rather, it's something that we should be able to switch into the signal chain with a press of a button, nod with satisfaction, and move on.
A mockup of the current interface with bypass switches instead of individual volume controls for each colour.[/caption] I've also reworked the circuit from the ground up, putting the colours in series rather than parallel and adding a master input drive control. This approach is taken directly from real-word recording practice. When a microphone signal travels through a preamp, and compressor to a tape machine, the coloration from those devices is not applied in parallel. Rather the harmonics generated by the preamp are modified by the compressor, which are then further tempered by the tape. Indeed, part of the art of being a tracking engineer is combining complementary pieces of gear into a signal path. Putting the modules in series makes Colour sound and behave more like a true recording chain.
The new working schematic , with colour modules placed in series with a single input drive control.[/caption] So, that's where are as of now. Circuit boards are already on order for the new design outlined above. If all goes well with this round of prototyping, hopefully I'll have a kit to offer very soon. As always, I welcome and appreciate your thoughts on this project. It's come as far as it has in no small part thanks to your feedback!
RM-5 Ribbon Mic Kit Limited Offer June 18, 2013 15:04 50 Comments
Last spring, microphone designer Artur Fisher and I collaborated to bring you a one-time kit offer for Artur's flagship RM-5 ribbon mic. Well, I'm glad to say that Artur is back for another run of his kits for the DIY community. Until July 7, 2013, Artur will be offering full and partial kits for the RM-5, including the new, custom-designed RTP-35 output transformer. RM-5 Assembly Manual
About the Microphone
The RM-5's excellence has been well documented by Recording Hacks, Rhythm in Mind, HomeRecording.com, and right here on the DIYRE blog. In short, it's is a great mic with the character one would expect of a well-designed ribbon. To quote myself: "rounded, almost tape-esque transients, a full low-end, and detailed, but gentle reproduction of the high-end." You can hear an electric guitar track I recorded with the RM-5 below. The RE-154 ribbon motor and RTP-35 output transformer are custom components designed to complement each other. Both are housed in a matte-polished, stainless steel. The assembled microphone retails for $395 USD.DIY Kit Offer
Both full and partial kits are available until July 7th, 2013. $10 worldwide, flat-rate shipping applies to all orders. All kits will be shipped by the end of August 2013; transformer-only orders will be shipped immediately. Kit Options:- RTP-35 Ribbon Mic Transformer $59
- Basic Kit: Transformer and RE-154 Ribbon Motor $115
- Full Kit: Transformer, Ribbon Motor, and Microphone Body $199
- Full Kit with Dedicated Shock Mount $235
Introducing the Passive Pickup Emulator (PPE) June 5, 2013 17:45 6 Comments

What does it do?
The PPE makes connecting your non-guitar gear to guitar amps and pedals sound "right." Like everything we do here at DIYRE, the PPE draws its magic from the dynamic, interdependent nature of analog electronics. When you connect two pieces of analog gear, they interact. Unlike a digital system in which data is transferred from one stage to the next unaffected, the signal passed between two analog devices is a unique result of the characteristics of both stages. So, one can't substitute one type of device for another and expect the same results.What's impedance got to do with it?
One of the most important characteristics of analog inputs and outputs is their impedance, often shortened as "Z." Modern gear is typically designed to minimize the sonic effects of impedance. Most guitar gear, on the other hand, takes a vintage approach (if it's not vintage to begin with) and embraces the effects of impedance. Guitar gear expects to see the wildly variable and complex output Z of a passive pickup and tone control. So it's no surprise that your guitar gear may sound a little flat or unnatural when fed a "modern" signal with a low, linear output Z.How does it work?
The PPE recreates the dynamic, interactive system of a guitar output using only four components. Looking at each of these in turn will provide a fairly complete explanation of how the circuit works.
L1 - 1 Henry Inductor
In a guitar pickup, the inductor converts the vibration of the strings into an electrical current. There are no vibrating strings in our emulator, but we use an inductor to recreate the pickup's phase and frequency non-linearities. In conjunction with the capacitor and resistors, the inductor creates a resonant low-pass filter.


Just like a Fender guitar, we use one leg of a potentiometer as the resistive element of our tone control. The rotation of the pot controls how much of the high frequency signal is thrown away by being shunted to ground.

How do I build it?
Full kits, including hard-to-source NOS 1H inductors, are available from the Store or you may choose to source your own parts. Either way, you can follow the step-by-step instructions in the PPE Assembly Manual. Estimated build time is 30 minutes to one hour.Building a Vintage-style U87 Mic Is Easier and Cheaper Than You Think (Video) April 30, 2013 11:43 35 Comments
In the video below, guest vlogger Matthew Jenkins walks us through his build of a vintage-style Neumann U87 clone. What some viewers may find surprising is that at no point during the video does Matthew perform any black magic or mortgage his home. As you'll see, a soldering iron, some attention to detail, $350-500 USD, and a free afternoon are all that's required to complete this project. And, thanks in large part to Microphone-Parts and Vintage Microphone PCB, all of the components that go into an excellent U87 reproduction are now available off the shelf. The components Matthew used are:- Microphone body ("donor" bodies range between $100-200 used or new)
- RK-87 capsule from Microphone-Parts ($109)
- D-U87 PCB Set from VintageMicrophonePCBKit ($20)
- PCB components from Mouser ($20)
- Cinemag CM-2480 from Cinemag ($43)
- Donor Bodies
- Behringer B2 (all switches)
- MXL 2010 (all switches)
- Aurycle A460 (no pickup pattern switch)
- MCA SP1 (no pickup pattern switch)
- CAD GXL2400 (no pickup pattern switch)
- Carvin CM87S (no pickup pattern switch)
- Gauge ECM 87 (no switches)
- Nady SCM 900 (no switches)
- Capsules
- Microphone Parts RK-87 ($109)
- Peluso P-K87i ($255)
- TSKGuy U87 ($250)
- Transformers
- AMI T13, designed specifically as a replacement for the original U87 transformer ($95)
5-Minute Project: How to build a "Circuit Sniffer" March 13, 2013 18:24 12 Comments
Here's a fun little noise-maker you can build for under $5 in under 5 minutes: a "Circuit Sniffer." Just as microphones pick up vibrations in the air and turn them into an alternating electrical current, this little device picks up the magnetic fields emitted by electronic devices. You can get some pretty brutal sounds by just plugging it into an amp and probing your household appliances. Check out the video below (4:09) to see what it does and how to build it.Sourcing component(s)
There is only one component involved here, an inductor. Inductors are measured in Henries; the higher their value, the greater a voltage they can induce from the same change in current. What this means for us is that higher value inductors will have a louder output and need less amplification. I used a 1000uH inductor in the video which is about the minimum value I would suggest to maintain a useful output level. Healthy-sized inductors often pop up in electronics surplus stores like All Electronics or Electronics Goldmine for less than a dollar each. Here are a couple that are available at the time of writing:- Electronics Goldmine G18221, 1000uH, 4 for $1
- Jameco 5800-103-RC-VP, 10000uH, $0.69
Designing a Headphone Amp for the Studio (Video) January 11, 2013 12:10 17 Comments

The "Colour" Project Pt. 3: Prototyping the Motherboard December 7, 2012 17:39 20 Comments
Making the Color Modules Larger
Our primary aim in making the distortion stages modular is to make "Colour" into an open platform for design and experimentation. With this in mind, we realized that we should make the modules as large as possible for more complex circuits and bigger toys like large caps, transformers, and optical cells. In order to make the modules bigger, however, we need to make some room on the motherboard. Most of the following revisions will probably make their way onto the 0.2 PCB:- Using DIP8 rectifiers instead of discrete diodes
- Changing mounting holes from #6 to #4 drill size
- Removing some of the test points
- Placing some low-profile components under the modules (.25" clearance)
- Using 16-pin IDC connectors rather than MTA for the stereo link
Standardizing the Connectors
Because we are opening up the color modules to third-party developers, it's essential that we specify a standard, off-the-shelf connector for mating the modules with the motherboard. We settled on 6-pin, single row, 0.1" (2.54mm) pitch pins and headers.These are the same used to plug Arduino "shields" into the motherboard and are available cheaply from countless parts distributors.
Arduino shield connected to motherboard
Rethinking the Interface
Since the concept phase, we've heard a lot of feedback, floated a lot of ideas, and even had some mildly heated debates about which controls to include on the front panel. The various controls we've at one point considered including are:- Input gain (master or for each module)
- Output trim
- Wet/dry mix for each module
- Bypass (master or for each module)
- Master bypass
- Three wet/dry mix controls (one for each module)
- Master output trim
- Master bypass switch
- "Saturation" Input drive switch
- Three module volume controls
- Dry signal volume
- Output trim
Dropping the "U"?"
Our working title seems to have some staying power. Nothing else we've thought of communicates the intent and use of the unit quite as succinctly as "Colour." But I just can't get used to typing that extra vowel. And even Link, whose Canadian tendencies inspired my choice for the British spelling, prefers the "more efficient" American spelling. I'm currently leaning towards dropping the 'u', but let me know in the comments if you have a strong (or even mild) preference.What's next?
The revisions we've looked at today all have to do with the motherboard. Next time we'll get into the actual "colors" with schematics and sound samples documenting our revision process for the modules. Thanks for following along while we slog through the gritty details!The "Colour" Project Pt. 2: Going Modular August 31, 2012 16:48 10 Comments
Then came the big "aha!" moment: we decided to make the distortion stages socketed, and therefore interchangeable.
The new design splits the circuit up into a motherboard, which provides the input, output, and control circuitry, and three daughter boards, which contain the various colors (distortion stages). This changes everything. The "Colour" we're designing now is not so much a single piece of gear as a platform for experimentation and discovery. The user will now have the option to choose which colors to include in her palette and, this being DIY after all, the ability to create her own. And the DIY community will have the opportunity to design and release their own "colours." In fact, there's reason these "colours" should be limited to distortion--almost any type of signal processing could be made into a module!
Next Week: The colours we're working on
Now that we've covered the motherboard in depth, we can jump into the sexy stuff next week when I'll detail the distortion stages Link is working on. In the meantime we'd like your help brainstorming a Wish List of signal processing modules you'd like to see. No idea is too crazy!
Many thanks to everyone who has expressed their enthusiasm for this project.
Designing a New Piece of Recording Gear Pt. 1: The Concept August 7, 2012 14:22 60 Comments
For a while, I had been on the lookout for a collaborator to work with to bring something utterly new to the DIY community. Someone with professional design chops who understood the DIY community and was open to the idea of making their designs open source. I was lucky enough to find Link Simpson by stumbling accross his Steller Studios DIY projects page. Expecting to find the usual gallery of completed kits and and guitar pedals, I found instead totally new designs for a preamp, compressor, personal headphone mixer, and more, all made from the ground up by Link himself. This was some next-level stuff! So I arranged a call and we began immediately throwing around project ideas.
What should we make?
I went into the brainstorming session with three main criteria for our new piece of audio gear:- Must be inexpensive, safe, and easy to build. Only modern, off-the-shelf components. No tubes or high voltages, avoiding AC power completely if possible. I wanted this project to be as newbie-friendly as possible.
- Not another clone, preamp, or compressor. I have only admiration and respect for the people who have brought great vintage clones to the DIY community, but that's not the direction I wanted to go with this project. Similarly, I don't think there will ever be a day when we have too many preamps or compressors (will there ever be too many craft beers? ice cream flavors?), but I wanted to do something more off-the-beaten-path.
- Something sexy. I'd had a lot of fun developing a passive summing kit and reamp box, but they weren't the kind of projects people were likely to drool over. I wanted our project to be something that would really capture peoples' imaginations and inspire them in the studio.
For a couple of weeks we tossed a ton of ideas back and forth, until Link astutely pointed out that most of my ideas included "the ability to push it hard for harmonic saturation." Why not--Link proposed--just focus on the harmonic saturation? Bingo.
"Harmonic distortion is sonic varnish." -Allen Farmelo
The Vision
We immediately began outlining a project that we're currently calling "Codename: Colour", a line-level harmonics generator with a variety of distortion stages that can be mixed in with the dry signal via independent wet/dry controls. Our vision is for a device that provides a range of subtle, yet distinctive "sonic varnishes" for your tracking and mixing palette. Because subtle harmonic saturation is often most effective when layered over multiple channels, our goal will be to make the Codename: Colour inexpensive enough that people can build numerous channels.Refining the Design
Now that we had our core idea, we faced another round of big decisions. "Which types of distortion?" "How should it be racked and powered?" "How should we balanced the output?" Etc... For today, I'll cover our current thinking in regards to the distortion types and powering/racking the unit.
Distortion Types
Link proposed a few different distortion stages:
- JFET, tube-like distortion
- Rectified, octaver-type
- Enhancer-type effect with treble-focused distortion
- Opamp/diode tape-like distortion
All of these would be achieved with sold-state, currently available parts, similar to the distortion stages in gear like the Empirical Labs Distressor or the Crane Song HEDD. One thing we agreed upon early on is that our goal with this unit would not be to emulate some "classic" sounds, such as "tape" or "triode," but to create sounds that we found beautiful or exciting. This is in line with our shared belief that words like 'tape' and 'tube' have been abused into meaninglessness by marketing departments.
Powering and Racking
As we weighed power supply options and priced out a run of metalwork, it became clear that developing an API 500-series module would allow us to focus more deeply on the audio circuit itself and make the unit affordable enough to mass produce. Indeed, the more experience I have with designing and dissecting audio gear, the more I come to the conclusion that modular formats such as the API 500-series and the 51x Alliance provide the best solution for most rack-mount gear. This is especially true for small manufacturers (DIYers being the smallest) who don't move enough volume to get bulk discounts on specialized components such as the power supply tranformer and metalwork. This is something that the DIY synth world has been onto for years and that, thankfully, is finally gaining ground in the recording community. I am, however, very reluctant to alienate those builders who don't have a 500-series rack, and I know how frustrating it is to see great gear released in a format you're not ready to commit to. So the final version of the PCB will certainly have a built-in option for racking the unit in a 1RU case.
What's Next?
In the next post, we'll delve deeper into the technical details of the circuit and pose some more specific questions about how the unit will operate. For now, we'd love to get your feedback on the core idea and features. Can you see yourself using something like this? Are there any important features you think we've overlooked? What do you think of the idea of ditching words like 'tape' and 'triode'?
How to Add a Guitar Pickup Emulator to Your LINE2AMP July 25, 2012 14:46 4 Comments
Note: This article is about an old, discontinued version of the L2A Reamplifier. The instructions below do not apply to the current kit.
The PPE mod equips your LINE2AMP reamping kit with a classic, single-coil pickup output which, in addition to providing a new tonal option, allows it to interface more "authentically" with vintage guitar amps and effects.
While browsing Jack Orman's excellent "Lab Notebook" series, I came across his drawing of a simple guitar pickup emulation circuit. This article and the Passive Pickup modification for the LINE2AMP are greatly indebted to Orman's article. There are three electrical properties we must recreate to mimic a guitar pickup: inductance, impedance, and capacitance. Accordingly, our passive emulator circuit consists of only three components--you guessed it: an inductor, a resistor, and a capacitor. Together, these components form an low-pass filter with a resonant peak that is largely responsible for the unique tonal signature of a passive pickup.
The component values in the LINE2AMP (pictured above) recreate the performance of a standard single-coil pickup. The inductor and capacitor set the cutoff value for the low-pass filter at 5.5kHz, while the resistor damps the ringing of the resonant peak. This creates a filter with a smooth bump around the resonant frequency and a gradual LPF after.
Approximate Frequency Response
Performing the Passive Pickup Mod

- Mount both output jacks in the chassis. This will keep the work steady and allow us to better gauge the wire lengths needed.
- Trim the leads of the inductor and a length of black wire according to the distance between the jacks.
- Place the 820pF capacitor between the two pins of the Passive jack.
- Place one of the inductor leads in the Tip pin and one end of the black wire in the Sleeve pin of the Passive jack. Solder the inductor, capacitor, and wire in place. (Illustration 1)
- Solder the remaining leads of the inductor and wire to their respective pins on the switching side of the Active jack.
Exactly How the LINE2AMP Reamping Box Works (and Why) July 19, 2012 13:30 19 Comments
Why do we need a reamping box? People have been plugging line-level signals into guitar amps since long before the first reamping box hit the market, often with good results. This is true; in many cases, simply plugging the output of your interface into an amp and crossing your fingers is good enough. However, what we want is to be able to plug any line-level device into any instrument-level input and have it sound right every time. In order to do this, we need a device that addresses the following issues:
- matching volume levels;
- interfacing balanced and unbalanced gear;
- emulating line and instrument impedances;
- ground-related noise.
As so rarely happens in audio and electronics, there is a cheap, simple, and ideal solution to all of these problems: an audio transformer. Let’s look at the ways a humble audio matching transformer can make reamping a consistent and transparent process.
Attenuating the Signal
The nominal level for a professional line-level signals is +4dBu, or approximately 1.2 Volts rms. Guitar signals, on the other hand, vary between a few tens of millivolts rms to 1 Vrms or slightly more depending on the pickup. So, in order to to mimic the output level of an average guitar, we need to attenuate our line-level signal somewhat before sending it to an amp. The clear choice for attenuating voltage (“volume” in audio) in terms of cost and complexity is a couple of resistors set up as a voltage divider. However, since we’re already using a transformer to address the other two problems of reamping, we might as well use it to reduce the voltage as well. Modified and reused under the GNU Free Documentation License
To understand how we can use a transformer to attenuate the signal, let’s look at how transformers work. Transformers operate according to a funny feature of our universe called “electromagnetism” by which a changing electrical field induces a changing magnetic field and vice-versa. A basic transformer such as the one we’re using consists of two coils of conductive wire wrapped around a magnetically permeable core, usually iron. The alternating current running through the “primary” (input) coil creates a magnetic field which induces a corresponding voltage in the “secondary” (output) coil. From our point of view, two important things happen to between the input and output of a transformer. 1) The grounds are isolated (which will be important for solving another reamping problem), and 2) the voltage, current, and impedance are transformed in proportion to the ratio between the number of turns of wire in the two coils (the “turns ratio”). Since the issue at hand is volume, let’s discuss voltage for the moment and leave current and impedance for later. Edcor PC10k/600 transformer
A transformer reduces or increases the voltage of a signal in direct proportion to the turns ratio. If the turns ratio is 2:1, the voltage induced in the secondary will be half of that in the primary. The Edcor PC10k/600 transformer included in the LINE2AMP kit has a turns ratio of 4.1:1, so the output signal is 4.1 times smaller than the input signal. In audio terms, this equates to 12dB of volume attenuation, just enough to get us to an average guitar output level.
Achieving the Correct Impedances
Put simply, “impedance” is the degree to which a circuit opposes the flow of AC current. Impedance is similar to the more basic concept of resistance, except that it is frequency dependent. That is, a circuit may present more opposition to high-frequency than low-frequency signals and vice versa. A great way to de-mystify impedance is to think of it in a realm we're all familiar with: acoustics. Every physical medium presents a certain amount impedance to the propagation of sound. This impedance is not uniform at all frequencies. This is why, for example, we hear the bass drums of a marching band first and higher frequencies connote "presence" to our ears.
There are two impedance values involved when connecting one piece of audio gear to another: that of the output device, called "source" or "output" impedance, and that of the input device, called "load" or "input." These two values tell us (at least) two important things:
- how much of the output signal (voltage) will be transferred to the input device;
- how much power is required for the output device to drive the input device.
Generally speaking, we get optimum results in both of these areas when the output Z is at least 8-10 times lower than the input Z; this is called "bridging" the output impedance. There is a common misconception that the input and output impedances should be matched--forget it, this is not true for audio! So what are the "correct" impedances in a reamping situation? The modern standard for line-level input Z is around 10kΩ, while guitar output Zs vary from below 100Ω for active pickups to 50kΩ+ for passive. In the same way that our transformer induces a different voltage across the secondaries than the primaries, it also transforms impedances. But whereas voltage is transformed in direct proportion to the turns ratio, impedance is transformed in proportion to the square of the turns ratio. Thus, the impedance ratio for our 4.1:1 transformer is 16.81:1, or approximately 10k:600.
We achieve our 10kΩ+ line-level input Z by placing a resistor across the transformer secondaries. The impedance reflected in the primaries is then 16.81 times the value of this resistor (for the LINE2AMP kit I have chosen a 1k resistor). At this point, with only the transformer and 1k resistor, our output Z is equal to the line-level output Z divided by 16.81, i.e., arbitrarily low. We can raise this value to within the range of a typical guitar output Z by adding a resistor in series with the output signal. I chose 15kΩ for this job but any value between 0 (no resistor) and 50k will emulate a different type of pickup.
Balanced to Unbalanced and Ground Noise
Reamping involves interfacing balanced (actually “differential” is correct, but I’ll defer to the parlance of our times) and unbalanced gear. A balanced connection has three parts: signal “hot” (non-inverted, +, tip, XLR pin 2), signal “cold” (inverted, -, ring, XLR pin 3), and ground (shield, chassis, sleeve, XLR pin 1). Balanced gear takes for its signal the difference between the hot and cold signals and ignores anything common to both (including noise). The chassis pin exists to provide unwanted noise a quick path to ground; it is not part of the audio signal.
Modified and reused under the Creative Commons Attribution-Share Alike 3.0 license.Original rendering by Søren Peo Pedersen
An unbalanced signal on the other hand consists of simply signal (tip) and common (“ground,” 0 V, sleeve). In an unbalanced system, the common is the reference for the signal voltage, so any noise injected into the common will in turn affect the signal. In the case of reamping, we are attempting to connect a balanced output from our mixer/interface/whathaveyou to an unbalanced, instrument input. What happens when we do this without properly "unbalancing" the output signal? By connecting the sleeve pins of both devices together we are connecting the the noise return path of the balanced output to the audio common of the unbalanced input. Noise, meet audio. Transformers solve this problem by providing what's called galvanic isolation between the input and output stages. Recall that transformers transfer voltage from one winding to the next through electromagnetic induction, without providing a path for current to flow. Thus, they allow the balanced output stage to "communicate" the signal to the unbalanced input stage without connecting their grounds/commons. It is therefore impossible to a ground loop to exist between the two devices. That's it. An elegant solution to a simple problem. Please feel free to continue this discussion below with your questions, comments or corrections.
Oktava MD-80M NOS Exclusive Offer July 13, 2012 09:23 22 Comments
A couple weeks ago, I received an intriguing email from my friend Artur Fisher (whos RM-5 ribbon mics many of you have now built). It went something like this: "Hey I've got an amazing deal on a small lot of vintage Oktava mics. Do you think the DIY crowd would be interested?" Needless to say, part of me wanted to shoot back "Yes" on the spot--"vintage," "Russian," "NOS," and "secret stock" are major trigger words for a recovering gear junkie--but I asked Artur to send me a pair to try out before I decided whether they were worth offering to you guys. I received my pair of Oktava HD-80M dynamic mics last week, just in time to try them out on a drum set and electric guitar session the next day. The guitarist and I were both impressed when I unpacked them. The aura of belonging to another place and time that these things put out is intense. The technical docs that come with each mic are completely in Russian, and though the pages are mint, they feel as though they might crumble in your hands. I felt a little India Jones-esque thrill as I pulled them gingerly out of their cases. It is a bit of a pain eluding the Russian cabalists who are now hot on my trail to recover these priceless artifacts that are at the heart of a worldwide, centuries-old conspiracy, but noone gets into audio engineering without expecting a little danger!
Anyhow, after sufficiently appreciating the their visual appeal, we put the 80Ms to work on snare and guitar amp. The first thing to notice about the sound of the 80Ms is that there is practically no low end. As you can see in the datasheet to the right, there is a steep low-end roll-off from 500Hz down. So right away we are in very unique territory--this is no Swiss army knife mic. Since there are very few instrumentes that don't have important stuff going on below 500Hz (and I never use a hi-hat mic), I tried pairing the 80M with a more full-bodied mic on the same source, similar to how Steven Albini use his old Altec mic on snare. For snare drum, I taped the 80M to a transformerless SM57, which lives on my snare by virtue of how well it captures the low-end body of the drum. The 80M does the opposite, and it does so really well. My usual practice with the SM57 on snare is to create a mult of the snare track, hi-pass and compress it with a slow attack time to emphasize the transient, and mix it back in with the original. The 80M essentially does this for me, with a little upper-mids excitement thrown in. As you can see in the waveforms below, there is a much greater contrast between the transient and the sustain with the Oktava than the SM57. Mixing this in with the signal from the SM57 brought out the attack in a way I'm not used to from a close snare mic. I'm glad I used strong tape when I attached the 80M to the SM57 because it's going to be there for a while.
For electric guitar, I simply moved our Shure/Oktava combo to the Sears Silvertone amp. As opposed to the snare, where I forsee using it on every session, the 80M is a more unique, oddball choice for guitar. Beyond just being brighter than the SM57, the 80M gave the guitar a heavy dose of "jangle"; mixing between the 57 and 80M signals was almost like mixing the neck and bridge pickups of the guitar. I know exactly what Tchad Blake meant when he said (I'm paraphrasing) "Sometimes you just can't mess up the guitar sound enough." Next time I feel that way, it's good to know I've got something special stowed away. I've only had the chance to use the 80Ms on one session, but I could imagine a few more uses for them:- A "telephone," band-passed vocal effect
- Hi-hat mic
- Beater-side bass drum mic
- Trashy, mid-range room mic (compressed to hell and back)
- Harmonica mic
How to Build a Boutique Passive DI June 29, 2012 19:12 31 Comments
Note: Full kits for our our passive DI project, the FE2, are now available in the store.
If you can solder one component to a couple of jacks, you can make the best passive DI money can buy. That's no exaggeration--at it's core, every passive DI is just a transformer, and some of the best winders in the world, Cinemag, Sowter, Lundahl and Jensen make transformers designed specifically for direct box applications.
Passive DI Basics
Let's start from the top: a DI, or "direct inject" or "direct box," is a device that allows one to plug an instrument output directly into a microphone preamp. A DI achieves this by doing two conversions: 1) from high impedance (Hi-Z) to low and 2) from unbalanced to balanced. Electronically, there are two ways (at least) to perform these conversions: 1) actively, with buffering/balancing circuitry or 2) passively, with an audio transformer. Active DIs are fairly complex, require power (usually in the form of +48Vdc "phantom power"), and are ideally suited for hi-Z signals such as those from passive guitar and bass pickups. Passive DIs are extremely simple, require no power, and are best suited for lo-Z inputs such as synthesizers and active pickups (however, they have been known to sound great on passive sources such as the "Billy Jean" bass line).
Why Go Passive?
From a technical perspective, active DIs outperform passive DIs in almost every respect, and at a fraction of the price. The performance of passive DIs is restricted by an inherent property of transformers: the closer you bring the input and output impedances to their ideal values, the more signal you loose. An active buffer, on the other hand, can present an exceptionally high input and low output impedance while maintaining unity gain. Yet here I am telling you how to build a passive DI. Pourquoi? They sound good. A good passive DI will thicken and smooth the sound in a way that a transformerless, active DI will not.
The DI Transformer
In terms of sound quality, the only component that matters in your passive DI is the transformer. And, unlike a reamping box where a budget transformer performs admirably, a direct box is a sensitive application that demands a high-quality transformer. There are a couple of essential features that take quality DI transformers out of the "budget" range: 1) mu-metal case for magnetic shielding and 2) Faraday shields to isolate each winding.
Building Your Direct Box
Gathering Components
Nothing exotic here. Transformers must be custom ordered from the manufacturers and the remaining components are standard at Mouser, Digikey, Farnell, etc. Depending on the transformer you choose, the entire BOM will cost you between $75 and $115 plus shipping from at least two locations.
Qty ![]() |
Value ![]() |
Note ![]() |
Approx. Price ![]() |
---|---|---|---|
2 | 1/4″ TRS jack | Solder terminals | $1 |
1 | SPST (or SPDT) Toggle Switch | Solder terminals | $1.25 |
1 | DI Transformer | Cinemag CM-DBX, Lundahl 1935, Jensen JT-DB, Sowter 4243 | $55 - $85 |
1 | Male XLR jack | Solder cup terminals | $3 |
1 | Aluminum chassis | Hammond 1590N1 | $11.50 |
1 | Ring Terminal | $.25 |
Assembly
Wiring
The schematic and wiring instructions below are based on the color coding of the Cinemag CM-DBX. However, the circuit itself applies to any DI transformer with a mu-metal case and shield wires for each winding. This includes offerings from Jensen, Sowter, and Lundahl.
- Begin by twisting the brown and red transformer leads together. (Making differential wires a twisted pair can reduce electro-magnetic interference.)
- Mount the transformer and jacks on the case. Stretch each transformer lead to where it will be soldered and trim the leads, leaving an extra 1/2" for wiggle room. Strip and tin the leads.
- Trim, strip, and tin two lengths of heavy-gauge wire for the ground connection. We'll call this wire "Green".
- Solder the leads to the jacks in the following configuration:
- Yellow -> Input Tip
- Orange, White, Black -> Input Sleeve
- Gray, Green -> XLR 1
- Red -> XLR 2
- Brown -> XLR 3
- Solder the green wire from XLR 1 to the center pin of the ground switch. Solder one end of the remaining length of green wire to one of the other pins of the ground switch, and the other end to the ring terminal.
- Fasten the ring terminal to the case to secure the chassis ground connection.
Looking for a full kit? We now offer the FE2 Passive DI kit in our store.
How to Add L/C/R Switches to a Passive Summing Box June 25, 2012 15:28 7 Comments
The theory of operation is simple: instead of each input being hard wired to either the L or R bus, the inputs go first to a switch which then sends the signal to either a) the L or R buss or b) both buses (or "center"). The wiring, however, is not so simple. Assembling these switches requires considerable point-to-point wiring skill and a good deal of patience. The following guide assumes you have an Endless Summer kit, however the general method can be applied to your own passive summing project.
Components
- Sort the 6.8k (blue, gray, black, brown, brown) and 9.53k (white, green, orange, brown, brown) resistors included in your kit. Each switch will use four 6.8k and eight 9.53k resistors.
- Trim two black and red pieces of hookup wire according to the distance between your switch and the jacks being switched, with a little extra length to account for the twisting. Strip and tin the ends of each wire.
Populating the Switch
- Place the hookup wires in the center row of pins, alternating black and red. Solder the wires to the pins and trim the leads. (Picture 1)
- Twist the pairs of hookup wires together tightly, leaving a 1/4" at the ends. (Picture 2)
- Place two 9.53k resistors in each pin of the bottom row so that the leads point out from the switch (away from the center row). Solder the resistors and trim the leads. (Picture 2)
- Do the same with the 6.8k resistors in the last remaining row of pins. Use only one resistor per pin. (Picture 3)
- Solder the hookup wires from the switch to the pins of the input jacks being switched. Solder the red wire to the Tip pin and the black wire to the Ring pin. (Picture 4)
Connecting the Switch to the Bus Wires
- Identify the two columns of pins associated with the each input jack. You will solder the 6.8k resistors from these columns to the bus wires that run directly above their respective jacks. Solder the resistor in the same column as the red wire to the "hot" bus wire and that in the black wire column to the "cold" bus wire. If you have already soldered the other, non-switching jacks to the bus wires, follow the standard you set regarding which wire is "hot" (Tip) and which is "cold" (Ring). Once you are done soldering, trim the leads. (Picture 1)
- Solder the 9.53k resistors in the same columns as a black wire to both of the "cold" bus wires and those in the red wire columns to both "hot" bus wires. At this point the wiring will become a bit of a rat's nest, and you may want to insulate the resistors from each other with the provided heat-shrink tubing. (Pictures 2, 3, 4)
Everything You Always Wanted to Know About Audio Electronics (But Were Afraid to Ask) May 30, 2012 12:45 60 Comments

Thanks for all the awesome questions! Stay tuned for the podcast.
One of the biggest obstacles for entry into the DIY community is that most of us arrive here from a music, not electronics background. We've all been there: you're planning your next DIY project and the documentation casually tells you to "bias the transistor." In that moment, very few of us want to be the one to ask, "umm.... what's biasing?" Well, now is your chance to ask all of those audio electronics questions you never found the right moment to ask! On Saturday, 6/9/2012 I'll be recording a podcast with a real live EE who has volunteered to answer your questions. Please post your questions in the comments section by Friday, 6/8 and we'll try to answer as many of them as we can. No question is too dumb or too complex to ask.About the Expert
Duncan Gray is an EE with over 30 years experience in the field, including a stint as a Senior Hardware Design Engineer for Digidesign. His areas of expertise include both analog and digital hardware design, audio transformers, power systems, and scientific programming. Many thanks in advance to Duncan for volunteering his time and expertise!May Giveaway: Hairball Audio Lola Mic Preamp Full Kit May 11, 2012 16:11 2 Comments
Dane Optical De-esser PCB/Chassis Offer April 19, 2012 22:18 2 Comments
For more info on the #31, see the XQP Audio website.
PCB features:
- All components are standard and currently available
- Includes on-board power supply and power transformer
- Fits in a 1RU, half-rack size chassis
- 1RU, half-rack size
- Two different color schemes: Green on anodized silver and gold on green. Sorry, no choosing--you get what you get!
- Serial number engraved on back panel (duplicates of commercially sold units)
- PCB slide-in slot
- May have minor paint-fill issues
- Includes a blank panel and mounting bracket to fill the space next to the de-esser
Talking Optical Compression with XQP Audio March 30, 2012 09:48 2 Comments
XQP Audio is a two-man audio company designing new, unique audio gear for the 500-series. Unlike other people I've interviewed, they don't make DIY kits, but they do run their business with more than a hint of DIY ethos--building units by hand, posting schematics on their website, and generally being openhanded with info about their circuits. When I called XQP out of the blue, Product Specialist Dane Tate made good on their slogan "Nice guys. Yes we are." by sending me a Disruptor to try out and walking me through the circuit in the video below. I learned a ton about vactrols, asymmetrical distortion, and how optical compression works. Hope you enjoy our geeky banter! Audio Samples: The following are samples of the 545 Optical Disruptor processing various instruments. Just as Dane says in the interview, this thing is great at making synths more lifelike. All of the samples are in the order of: 1) Clean, original audio 2) Medium disruption 3) All the way up!DIY DAW Controller Part 1: Choosing a MIDI Interface March 19, 2012 17:39 27 Comments
While wrapping up a mammoth "in-the-box" (computer-based) mixing session the other week, I vowed that I would not mix another project without some real faders under my fingers. Around this same time, an email subscriber tipped me off to the amazing open-source MIDI controller projects happening at midibox.org. Usually when people think MIDI they think of sequencers, keyboards, synth controllers, etc., but basically anything we do within a DAW (Digital Audio Workstation: ProTools, Cubase, Logic, etc.) can be controlled via MIDI. Indeed, many commercial control surfaces such as the Behringer BCF2000 are MIDI controllers. So, I've got the itch to make my own DAW controller. Great! Right now that's about all I've got. I know next-to-nothing about MIDI (or anything digital for that matter), and the MIDIbox website makes about as much sense as Greek Alphabet soup after a couple hours of browsing. I do know, however, that I've been through this before--I couldn't have told you whether audio signals were AC or DC when I built my first preamp. This time around, I'm going to document every step of my climb up the MIDI learning curve in hopes that it will take some of the mystery out of building your own DAW controller for those standing on the sidelines.
The Grand Vision
Since this is my first foray into MIDI, I'm planning on doing something fairly simple that would nonetheless break me out of the box for most of my mixing needs. There are 16 channels with pan, volume, mute, solo, and two aux sends each. That's 64 potentiometers total (16 slide + 48 rotary) and 32 switches.
I'm still debating whether to use motorized or normal faders. It would be great to bring up a session in my DAW and have all of the faders snap to the corresponding positions. But motor faders are at least 5x more expensive than the normal ones. At this point, I'm leaning towards regular faders to keep the cost low. What do you think, will I regret this down the road? I've never mixed a project on a console or control surface without motorized faders before, is it a huge workflow problem not to be able to see where your levels are by looking at the faders?
Choosing a MIDI Interface
After a bit of research, the two MIDI platforms I'm looking at are Doepfer "Pocket Electronic," Doepfer USB64, MIDIbox 64, and MIDIbox LC.Doepfer MIDI Interfaces
The Doepfer products are appealing because they come as assembled, pre-programmed analog/MIDI interfaces. The Pocket Electronic puts out up to 16 channels via MIDI jack, while the USB64 can do up to 64 via USB. The Pocket Electronic seems like a great solution for a simple 8 faders + pan pots setup, but is decidedly short on channels for what I want to do. The USB64 offers enough channels and the option for digital inputs, which can be used for solo/mute switches. However, as far as I can tell, the USB64 can operate only in digital or analog mode, not both. Meaning I can have pots or switches, but not pots and switches. So, while the Doepfer units look very appealing from a digital newbie's perspective, they're not quite right for what I want to achieve.
The MIDIbox Platform
MIDIbox is an open source, modular MIDI platform that, while it's pretty confusing to me still, appears to be extremely flexible and scalable. Basically, there is a core "brain" circuit board that takes inputs from different modules (analog input module, digital input module, etc.) and turns them into MIDI I/O. People configure these modules in all sorts of ways with different firmware to create things like sequencers, DJ control stations, synth controllers, and of course DAW controllers. I'm sure that is a gross simplification of the MIDIbox system, but it's what I've been able to figure out so far. (Please feel free to correct or englighten me in the comments.) Circuit board layouts and firmware downloads are available at ucapps.de, and PCBs/kits are available from the MIDIbox shop. Of the many MIDIbox permutaions available, those that seem most applicable are the MIDIbox LC and the MIDIbox 64. The LC emulates the performance of the Logic Control / Mackie Control surfaces. If I were building the Ultimate DAW Controller, I would probably go with this as it allows for motorized faders, but since it uses the LC (or MCU) format, I'm not sure it's compatible with my DAW of choice, Reaper MIDIbox 64 is an older project, which appears to have been replaced by the MIDIO128, but since the Midibox Store stocks only the 64 PCBs at the moment I think I'll go with that. The 64 allows for up to 64 pots/faders, 64 switches, and 64 LEDs. More than enough to realize my "Grand Vision." There is also support for an LC-display and other stuff, but I'm going to ignore those for this project in the interest of keeping things simple.
What's Next
Right now I'm leaning towards the MIDIbox 64, but I'm going to continue reading about the MIDIbox platform until I start involuntarily piecing together interfaces in my head as a I fall asleep (usually a good sign I've reached a critical level of obsessiveness with a project). Once I settle on a configuration, I should be able to assemble a rough bill of materials and price out the project in Part 2. Until then, if you have any experience with MIDI DAW controllers, I'd love to get your feedback on which/how many controls you feel are essential for mixing, especially how you work with or without motorized faders.
DIYAC Ribbon Mic Kit One Time Offer March 6, 2012 22:58 54 Comments
This month, I'm glad to be able to offer an exclusive DIY kit from ribbon mic designer Artur Fisher of DIY Audio Components (DIYAC). The kit is for Artur's RM-5 microphone, which I reviewed here and Jordan Reynolds reviewed for RecordingHacks. The RM-5 is a great mic, and I'm thrilled that Artur is offering it as a kit to the DIY community. However, he's only doing one run of kits and closing the pre-order on April 5th. You can order directly from DIYAC through the PayPal button below.
Some words on the kit from Artur:
- The RM-5 product page
- DIY ribbon design notes
DIY Mic Preamp Design: Interview with Mike Mabie of Hairball Audio March 2, 2012 10:38 1 Comment
Sometime this month (March '12), Hairball Audio will drop a totally new mic preamp design called the "Lola." It's rare enough that we see an original design made specifically for the DIY world, so I wanted to talk to Mike about how it came about and what's involved in the design. The Lola is unique in being a fully differential design with input/output transformers and discrete opamps. Don't worry, Mike explains what "fully differential" means in the interview!
The Lola's fully differential design is derived from the "Double Balanced" mic pre design of Graeme Cohen. There's a lot of good stuff about Cohen and his preamp design at Leon Audio's website. Full and partial kits for the Lola will be available from Hairball Audio's website. Many thanks to Mike for granting me this interview!
LINE2AMP Design Journey February 15, 2012 20:14 1 Comment
This all started when my grandfather decided to dissolve his woodworking shop and give me his gorgeous old Sears drill press. I couldn't let a tool like that sit idle in my basement, so I thought, hey why not make a DIY kit? That was last August (2011), and while the The LINE2AMP reamping box is about as simple a piece of gear can get, it's been a rather long and circuitous journey to bring it to fruition. Doubtless, someone more experienced could have whipped the LINE2AMP up in a weekend, but I've learned a ton about electronics, product design, and DIY in the past few months. I'll be using this page to share what I've learned with you, as well as to let you in on the design process of the LINE2AMP as it progress.
August 2011: Researching Reamping
My original goals for the LINE2AMP were that it should:- Perform as well as any commercially available unit
- Cost less than $50 to build
- Be simple enough for newbies to build successfully.
I starting looking around at other reamping designs available on the internet and found three popular schematics: Jensen, Recording Magazine (Scott Dorsey), and NYDave. Looking at schematics the schematics, I realized that all of them shared the same essential topology:
I ordered a couple of transformers from Edcor USA to start experimenting with circuits.
September 2011: Prototyping
Four weeks later transformers arrived and I started soldering. 30 minutes later I had a working reamping box. Huzzah! Goal #3 was in the bag. My first prototype hewed almost exactly to NYDave's design: I used the Edcor PC10k/150 transformer with a volume pot and 200 Ohm terminating resistor. The only variation was that I used a 1M Ohm variable resistor to test different output impedances. Testing the prototype with a variety of amps, pedals, and DIs revealed a few things:- The unit was dead quiet and imparted practically nothing on the tone. At first, I had been skeptical about how the unshielded Edcor would perform, as both the Jensen schematic and the Reamp use shielded transformers. While a shielded trafo would certainly be better on paper, in practice the Edcor added no noticeable noise, even when run via DI into a clean preamp.
- The impedance resistor had no noticeable effect on the sound until it was cranked beyond about 200k Ohms, after which the signal started to lose some high frequencies and become distorted in the bass.
- In almost all cases, there was less noise when the connection from ground pin of the input jack to the case was disconnected. Only with some pedals did it sound better connected.
Overall, I was really happy with how the circuit worked. I didn't have a commercial reamping box on hand to shoot it out against, but it did everything a reamping box should and without any noise or sonic artifacts of its own. In fact, I was pretty blown away by the transparency of the Edcor transformer. In a blind test between A) a signal sent first to the reamping box, then the DI input of my Hamptone preamps and B) a signal sent right from my interface to the line input of the Hamptones, I couldn't make any conclusive distinction between the reamped and non-reamped signal.
Paring Down to Essentials
After playing around with my prototype, I realized that the LINE2AMP could be made even simpler than any of the other reamping designs and do the job just as well. The first thing to go was the impedance knob. From one perspective, it makes sense to have a range of output impedance available to emulate the source impedances of different guitars (typically between 10k-50k Ohms) and pedals (as little as 200 Ohms with a buffered output). However, in testing there was no audible change in tone until about 200k Ohms. From a technical perspective this makes sense, as any source impedance below 100k or so would be easily bridged by most guitar amp and pedal inputs. Goodbye to that pot! Next to go was the volume knob. In theory it's nice to have a tactile way to control the level, but in practice I found myself almost always doing it from the DAW. I also rarely found myself wanting less signal, and without adding active circuitry the volume control can only attenuate, not boost. What's left is the bare essentials of a reamping device: a transformer for impedance/voltage conversion and ground isolation, and a resistor to set the input/output impedances. That's it!Work in Progress: The Ultimate Audio Transformer List December 9, 2011 17:37 12 Comments
How awesome would it be to have a list of every transformer you'd ever want to use in a DIY project? Let's do it! Please leave your contributions in the comments section. Thank you to Justin Boland for getting us started.Manufacturer | Part # | Type | Turns Ratio | Impedance Ratio | Used By |
---|---|---|---|---|---|
Carnhill | VTB9045 | Mic In | Neve | ||
Marinair | 10468 | Mic In | Neve | ||
Ed Anderson | EA10468 | Mic In | Neve | ||
Sowter | 9145, 9165 | Mic In | Neve | ||
Carnhill | CA-18-VTB9071 | Line In | Neve | ||
Marinair | LO-1166 | Line Out | Neve | ||
Marinair | LO-2567 | Line Out | Neve | ||
Carnhill | VTB1148, VTB1847, VTB9049 | Line Out | Neve, Trident | ||
Ed Anderson | EA1166 | Line Out | Neve | ||
Sowter | 8751, 9160 | Line Out | Neve | ||
Sowter | 9780 | Line Out | Neve | ||
Cinemag | CMOQ-2S | Line Out | Neve | ||
Crimson Audio | CT-2385 | Line Out | Neve | ||
JLM Audio | JLM111DC | Line Out | Neve, Trident | ||
API | 2622 | Mic In | 1+1:7 | 150/600:10k | API |
Ed Anderson | EA2622 | Mic In | 1+1:7 | 150/600:10k | API |
Cinemag | CMMI-8PCA | Mic In | 1:8 | 150:10K | API |
Sowter | 9820 | Mic In | 1:4.37 | 150/600:11.5k | API |
API | 2503 | Line Out | 1:1, 1:2, 1:3 | 75:75, 75:300, 75:600 | API |
API | 2623 | Line Out | 1:1, 1:2 | 75:75, 75:300 | API |
Ed Anderson | EA2623-1, EA2623-4 | Line Out | 1:1, 1:2 | 75:75, 75:300 | API |
Ed Anderson | EA2503 | Line Out | 1:1, 1:2, 1:3 | 75:75, 75:300, 75:600 | API |
Sowter | 9825 | Line Out | 1+1+1+1 | 75:300+75 | API |
Cinemag | CMOQ-2L | Line Out | 1:1 | API | |
API | 2164 | Line In | 10k:600 | API | |
Jensen | JT-16-B | Mic In | 1:2 | 150:600 | John Hardy |
Jensen | JT-11-BMQ | Line Out | 1:1 | 600:600 | John Hardy |
Jensen | JE-6110K-APC | Mic In | 600:150/10k | Auditronics | |
Jensen | JE-123-S | Line Out | 1:1 | 600:600 | Auditronics |
Sphere | 7341 | Mic In | Sphere | ||
ZUTT | 012A, 782A | Mic In | 1:5.63 | 1.2k:38k | Trident A, B, and Fleximix* |
ZUTT | 783A | Line In | 1:1 | 15k:15k | Trident A, B, and Fleximix* |
Sowter | 7456 | Mic In | 1:5.9 | 600/30K | Trident |
Jensen | JT-13K7-A | Mic In | 1:5 | 150:3.8k | Trident |
Sowter | 3553, 2318, 3777 | Mic In | Calrec* | ||
Sowter | 3955 | Line Out | 1:1.06 | 600:600 | Calrec* |
Triad | A-67J | Mic/Line In | Spectra Sonics* | ||
Triad | HS56 | Mic/Line In | 1:1 | 600:600 | Pultec, Spectra Sonics |
Sowter | 3603 | Mic/Line In | 1:1 | 600:600 | Pultec, Spectra Sonics |
UTC | LS30 | Mic/Line In | Spectra Sonics | ||
Triad | HS66 | Line Out | Spectra Sonics* | ||
St. Ives | VT22670 | Mic In | Neve* | ||
St. Ives | VT22671 | Mic In | Neve* | ||
Marinair | T1422, T1442, T1452 | Line In | Neve* | ||
UA | 5002 | Line Out | UREI 1176 Rev A-E* | ||
Bournes | B11148 | Line Out | UREI 1176 Rev F-H | ||
UTC | 012 | Line In | UREI 1176 | ||
Jensen | JT16A | Mic In | Sunset Sound Console | ||
Edcor | PC10k/150 | Line Matching | 8.2:1 | 10k:150 | LINE2AMP Reamping Box |
Cinemag | CM-9888 | Mic Out | 1:28 | Ribbon mic | |
Lundahl | LL2912 | Mic Out | 1:37 | Ribbon mic | |
Sowter | 8074 | Mic Out | 1:40 | Ribbon mic | |
Edcor | RMX1 | Mic Out | 1:37 | Ribbon mic | |
AMI/TAB Funkenwerk | T42 | Mic Out | 1:42 | Ribbon mic | |
AMI/TAB Funkenwerk | T58 | Mic Out | Shure SM57/SM58 Mod | ||
Samar Audio | RT36 | Mic Out | 1:40 | Ribbon Mic | |
Monacor | LTR-110 | Line Matching | 1:1, 2:1 | ||
Monacor | DIB-110 | Direct Box | 10:1 | ||
Lundahl | LL1538 | Mic In | 1:5 | Focusrite, Trident, GP Electronics | |
Lundahl | LL1517 | Line Out | 1 + 1:1 + 1 | Calrec | |
Altran | C-3837-1 | Line In | 1.58:1 | 500:200Ω | DIY 1176 |
How to Build a DIY Passive Summing Box December 8, 2011 12:13 105 Comments
I've been curious for a while about the fuss surrounding analog summing. But with commercial boxes priced $600+ I wasn't that curious. Luckily, passive summing is a pretty simple concept and one that's very wallet- and DIY-friendly to achieve. Check out the video above for a quick run-through of how I built my 16-channel summing box.
How It Works
Most analog summing designs take a number of mono inputs and assign them to the stereo bus via either pan pots or L-C-R switches. This route, while superior in functionality, is rather complex and expensive. The design below leaves out panning/assigning and makeup gain in order to avoid the need for power and forgo toggle switches (≈$7.50/channel). What we end up with is a passive bus mixer: 4 or 8 stereo pairs are summed via L and R buses, which are then sent to external microphone preamps for makeup gain. This basic design has been proposed by "New York Dave" and Fred Forsell, and can be found in the monitor section of old Neve consoles.
The greatest benefit of this approach, in my opinion, is the tonal flexibility. Every pair of preamps will impart their own sonic signature on your mix.
Inputs are summed to the bus wires via resistors. All of these resistors must be the exact same value with as low a tolerance as possible. Recommended values are between 5-10k ohms depending on the input impedance and volume drop you're aiming for. The value of the shunt resistors depends on the number of inputs used and the value of your summing resistors. NYD gives us the formula for calculating it, where I is the input impedance, R the desired output impedance, and N the number of channels: (I/N)*R/((I/N)-R)
Putting It Together
Building a passive summing box always seemed like a bit more of a hassle than it should be for such a simple circuit until I found Rhythm in Mind's idea for mounting everything on a front panel. It's a great approach for this project, as all of the components weigh in at a grand total of around 3 lbs. Simply drill a panel as I've drawn below (or order one!) and mount components right to the panel as shown. I used nylon standoffs to suspend the bus wires with lock washers to hold them taut.
I've had no problems with noise or interference with this setup. But if you do find it to be noisy, you can always add a case.Bill of Materials
Qty | Value | Note |
---|---|---|
8 | 1/4" TRS jack | Panel mount, solder terminals |
2 | 182Ω for 16ch 165Ω for 8ch | Metal film, 1/4 watt, 1% tolerance resistor |
16/32 | 6.8kΩ | Metal film, 1/4 watt, 1% tolerance resistor |
4' | Bus wire | At least 24 AWG thickness |
6 | 1 3/8" Nylon standoff | Female->male, 6-32 or 4-40 thread (must match other standoff) |
6 | 3/8" Nylon standoff | Female->male, 6-32 or 4-40 thread (must match other standoff) |
6 | Machine nut | 6-32 or 4-40 thread (must match standoffs) |
6 | Lock washer | #6 or #4 size (must match standoffs) |
2 | Male XLR jack | Solder cup terminals |
4 | 4-40 nuts and bolts | For mounting XLR jacks |
Using It
Since the inputs of our summing panel are hard wired to either the L or R bus, you can't simply send a mono signal (unless you want it panned R or L). Rather, assign your tracks to a number of stereo buses and then send those buses to the summing panel as shown below:
Update: Adding Mono Inputs
Since posting this article, I've received a lot of questions about adding mono inputs for tracks like lead vocal, bass, kick, and snare that are often panned dead center. Luckily, this is really easy to implement with just a little more math. Of course we know that in the world of stereo, a signal that is "dead center" is actually two identical signals of the same volume in each channel. So instead of sending our mono inputs to either the L or R buss wires, we will send them to both. However, by doubling the signal, we've made our mono input 3dB louder than the others. We can rectify this by changing the input resistor values for the mono channel to 1.4x the value of the regular input resistors (1.4:1 being 3dB expressed as a ratio).
DIY Kits
We now stock the SB2 Passive Summing Mixer kits in the DIYRE store. The SB2 accepts 8 or 16 balanced inputs via D-sub jacks and puts out two balanced, microphone level outputs. The kit contains everything you need to build a passive summing mixer. SB2 Passive Summing Mixer Kit $49
I.J. Research 4KCC Build Guide November 22, 2011 16:30 12 Comments
The IJ Research 4KCC is now sold by Ramshackle Recording.
Introducing: LINE2PRE Re-Preamp November 18, 2011 19:19 13 Comments
The LINE2PRE is a tool for sending your pre-recorded tracks through your mic preamps for additional harmonic saturation. Why hasn't anyone thought of this before?Reamping boxes like the LINE2AMP are a great studio tool for those who have a lot of amps, pedals, and other guitar-level gear lying around. Well, I dunno about you, but, being a recording engineer, I've invested a lot of more in awesome mic preamps than in guitar gear. And as well all know, a preamp that overdrives nicely is one of nature's finest signal processors. So I put together this little box that basically performs the same function as the LINE2AMP, but with a little extra volume reduction, an output impedance tailored to mic preamps, and an XLR output jack. Exceedingly simple, but it does it's job quietly and with pretty much zero sonic fingerprint.
Full kits and assembly instructions for the LINE2PRE will be available in the store in early 2015.
Test Driving the DIYAC RM-5 Ribbon Mic (+how to build your own for <$100) November 7, 2011 12:28 7 Comments
A couple of weekends ago, I attended a friend's birthday at the Latvian society of Philadelphia. Knowing almost nothing about Latvia except the excellent microphones of Juris Zarins (Violet) and my friend Artur Fisher (which I'll get to in a second), I picked the bartender's brain about his home country while I sipped my first Latvian beer. Turned out Latvia's history was fascinating enough to keep me riveted to my bar stool for an hour or two while the party raged at increasing volume around me. For instance, did you know that the class that entered university this year were the first to have been born in the modern state of Latvia?
But I digress... this post is about microphones! My unplanned introduction to Latvian culture and beer turned out to be of the fortuitous kind, as just the week before I had received one of Artur Fisher's RM-5 ribbon microphones to try out. Artur's microphones are made by hand (in Latvia, of course) with his own RE-154 ribbon motor. Visually, the RM-5 is right up my alley: elegant, simple, utilitarian, and unbranded. Sonically, it delivers everything I had imagined a high-end ribbon mic should: rounded, almost tape-esque transients, a full low-end, and detailed, but gentle reproduction of the high-end. The track below was recorded with the RM-5 only, with no EQ and very moderate compression. So what does this mean for DIY? You can build your own microphone with Artur's RE-154 ribbon for about $100. Here's what you need:
- Artur's RE-154 Ribbon Motor $59
- Edcor RMX1 Transformer $22.77 (same transformer used in the RM-5
- Male XLR Connector ≈$3
- Microphone body, be creative!
As you heard above, you'll end up with a great mic. Being able to build it for the price of an SM57 is, to my mind, almost absurd. Absurdly awesome. Long live DIY!
How to Build a DIY Reamping Box October 3, 2011 13:52 30 Comments
One of the most powerful tools for expanding your sonic pallet in the studio is a reamping box--a box that converts the output from your mixer/interface/tape machine to an instrument-level signal. Suddenly, all of your guitar amps, effects pedals, and synthesizers become effects for any signal you can throw at them. A reamping box is a great first-project for DIY beginners: it's totally passive (you can't shock yourself), there are a limited number of solder joints to make, and there's plenty of room to make those joints. For a better idea of what's involved in this build, check out the following video on how to make a simple reamping box: Full kits for our popular reamping box, the LINE2AMP, are available from the store. For full assembly instructions, please see the LINE2AMP assembly guide.How to Make Your Own XLR Mic Cables September 3, 2011 19:28 12 Comments
Soldering your own microphone cables is one of the most satisfying DIY projects you can undertake. No kidding! There are few things more gratifying than slicing through the soft rubber coating with an x-acto knife and joining the conductors to the connector with perfectly shiny solder joints. On top of that, building cables is a great way to get your feet wet soldering, and it's one of only DIY projects that is guaranteed to save you money. Check it out:- A 20' Monster P500M20 XLR Cable from Sweetwater costs $59.95.
- A higher quality DIY cable using Canare Quad Core and Neutrik XLR connectors costs less than $12.
That's almost $50 saved on one cable! Imagine how much you'll save over a lifetime simply by learning to solder your own cables.
Here are the components I recommend using:
- Cable: Canare L-4E6S Quad Mic Cable
- Canare's quad core cable uses two conductors for each audio signal (hot and cold) and a woven shield to reduce noise and improve flexibility. You can go with Mogami cable if you're inclined, but I've found the Canare to be excellent for half the price
- Available from Redco Audio
- Connectors: Neutrik X-Series (silver contacts)
- Neutrik has an extensive line of connectors, but I stick with the X-series because they're what I've used in the past and they haven't failed me yet (plus they're the cheapest). I opt for the silver contacts because, while the gold is resistant to corrosion, the gold plating tends to wear off after a few hundred plugs and unplugs anyway.
- Available from Redco, Mouser, and pretty much anywhere components are sold.
New Feature: Pre-Orders for Old Projects! August 30, 2011 14:33
Have you ever discovered an awesome project only to find that PCBs and kits haven't been offered for years? I get comments and emails weekly from people trying to track down products that are no longer in production. I also hear from designers who would be more than willing to do another run of kits, pcbs, front panels, etc. if they could be sure the interest was there to make back their investment. So today I'm introducing a new feature that will connect interested builders with those who can offer kits and pcbs. If you're interested in a new run of kits or pcbs for a certain project, simply navigate to the page for that project and enter your info in the pre-order form. Once enough people have expressed interest in that project, the designer will contact you about prices, shipping, etc. Of course there's no guarantee that PCB files, front panel art, etc. will be available to fulfill a pre-order for every project, but by that same token, you are not obligated to buy anything by simply leaving your contact info.Forgotten and Obscure DIY Link Roundup August 25, 2011 14:27
When I started this site a year ago, I reckoned there were maybe 100 or 150 recording-related DIY projects on the web to dig up and document. Hah! Let's all share a laugh on the naïveté of 2010 Peterson. To date, there are 228 projects in the directory, with at least 5 more discovered or created every day and added to the already-staggering backlog. Please enjoy these golden favorites from said backlog:
A shrine to the RCA MI-12188A, including instructions for restoring and modifying this 50's public-address amp.
A piezo pickup made literally from scratch. This build doesn't have a bill of materials, it has a recipe.
A clever adaptation of Rod Elliott's pink noise generator that runs on +48vdc phantom power and fits in an XLR barrel adaptor. Pink noise is a great tool for testing playback equipment and room acoustics.
NRG Recording's Soundcraft 2400 channel strip build. This is the first and only Soundcraft DIY project I've seen. Kudos to Frank for a unique and great-looking build.
DIY tape echo using old cassette heads. Brilliant!
The genius behind this sound generator build wins the "Classy Chassis" of the year award for his creative use of a warped vinyl record.
Simple Guide to DIY Electronics #1: Passive Components August 16, 2011 16:31
Electronic components are called 'passive' when they don't produce gain or require a power supply to function. While there are numerous components that meet this definition, when we refer to 'passive components' we usually mean the following three types: resistors, diodes, and capacitors.
Resistors
Resistors are those little, candy-looking tubes that populate almost every audio project in great numbers. Their job is to present a certain amount of opposition, or resistance, to the electrical current flowing through them. There are three specifications you'll use to identify the correct resistor for a certain job:- Resistance: The amount of resistance, measured in in Ohms (Ω). This is usually indicated on the surface of the resistor with color-coded stripes.
- Tolerance: The degree of precision to which the resistor was manufactured. For example, a 1k resistor manufactured to ±1% tolerance may have an actual value between 990 and 1.1k ohms. This is also typically indicated with a color-coded stripe.
- Power: The maximum power (heat) a resistor can dissipate without being damaged. This is not specified on the body of most resistors, but can often be guessed from the resistor's physical size with a little experience. Most resistors in audio circuits dissipate less than 1/2 Watt of power.
- Resistive Material: Resistors are made from a wide range of materials, but the most common in audio circuits are:
-
Metal Film: By far the most common in modern equipment. They are nearly transparent in audio circuits and can be made cheaply to very strict tolerances.
-
Carbon Composition: Long since surpassed by film resistors in terms of noise and precision, carbon comps are nonetheless still used, especially in circuits that attempt to clone a vintage unit. Many vintage guitar pedal enthusiasts, for example, use exclusively carbon comps.
-
Carbon Film: Precise and low-noise enough for most audio applications. Often used when a certain value or power rating is not available in metal film.
Capacitors
Capacitors ("caps" for short) are the second most common component in audio projects. They are designed to store and discharge a certain amount of energy and play a wide range of roles in circuits, from smoothing power to filtering frequencies from an audio signal. There are three important specs that define a capacitor:- Capactiance: The amount of capacitance, measured in farads. Common subdivisions of the farad are micro-farads (uF) nano-farads (nF) and pico-farads (pF).
- Voltage: The maximum operating voltage.
- Polarity: Some capacitors are polarized and must be installed a certain way in order to remain in their "unexploded" state :O If a capacitor is polarized, its polarity will be marked on the body of the capacitor and accordingly on the schematic or PCB in which it is used.
-
Ceramic: Small, non-polarized, usually used as bypass caps.
-
Electrolytic: Capable of high capacitance per volume, usually polarized.
-
Silver Mica: Linear and stable, but relatively large and expensive.
-
Polyester: Low tolerance and low voltage, often seen in audio circuits.
-
Polystyrene: High stability, low distortion.
Diodes
Diodes are components that allow current to flow through them in only one direction. A diode's two leads, the anode and the cathode, will usually be labeled and must be installed correctly in order for the diode to work properly. Common types of diodes found in audio projects are:-
Light Emitting Diode: Emits light when current passes through it. The anode is indicated by having a longer lead than the cathode.
-
Schottky Diode: Designed to cause as little voltage drop as possible. The cathode is usually marked with a silver stripe on the diode's body.
-
Zener Diode: Operates like a standard diode until a certain voltage is reached, when it allows current to flow both ways. The cathode is usually marked with a stripe.
- The noob's guide to DIY jargon.
- It's hard to beat Rod Elliott's beginners' guide to electronics, also written from an analog audio perspective.
Shure SM57 / SM58 Mods August 8, 2011 17:16 1 Comment
Unless you've been operating your recording studio from under a rock since 1965 (or are one of those curmudgeonly "haters") you've probably got an SM57 or SM58 in your mic locker. With their screw-open bodies, these mics are exceedingly simple and rewarding to mod.Removing the Transformer (the "TapeOp Mod")
The stock transformer in the SM57 increases the output level by about 12dB, but it also contributes to the 57's somewhat pinched and midrangey sound. Taking it out is a quick and free way to increase the frequency and transient response of your mic. The video below walks you through the steps for this mod:TAB-Funkenwerk Transformer Swap
TAB-Funkenwerk, maker of fine vintage condenser microphone kits, manufactures a replacement for the stock SM57/58 transformer. The T58 transformer is designed to maintain the basic SM57 sound while extending the high and low frequency response. T58s are available from for $80 each.
The Impedance Mod
Nowadays, most mic preamps and mixers present a rather high input impedance for condenser microphones. However, the SM57 was designed in the days of the standard 600ohm input and theoretically performs better when more heavily loaded (lower input impedance). By connecting a resistor across the preamp's input, we can increase the load on the SM57. In his Recording Magazine article (link below), Paul Stamler provides the following formula for calculating the resistor, where Rg is resistor to be strapped across the input, Rd is the desired input impedance, and Ra is the actual impedance of the preamp or mixer: 1/Rg = 1/Zd – 1/Za. The mod can be built into the male plug of an xlr cable or an xlr barrel connector by soldering a resistor between pins 2 and 3. Alternatively a simple box with a 1k linear resistor would provide a good range of impedances for different inputs.Alesis 3630 Compressor Mods July 26, 2011 11:55 6 Comments
Touted officially by Alesis as the "most popular dynamics processor ever made," the 3630 is a bargain bin compressor that can be polished to resemble a professional one. The circuit employs some solid design fundamentals, but by all accounts suffers from inferior components and design choices. Various mods have been proposed over the years to considerably expand the sweet spot the 3630, lower its noise floor, and remove the snaps, crackles, and pops the stock unit is prone to. Collected here are those mods that have been deemed the most successful by the people who have tried them. Many thanks go to the originators of these mods who have shared their research with the DIY community.
"The 3630 is basically a dbx compressor. It uses dbx-designed RMS level sensors and VCA gain-change chips. Problem is, most folks have not taken the time to learn how to use this box, find the sweet spots for level setting, gain reduction, gain make up and attack / release times." -Michael Joly via Gearslutz
"I'm not saying that if you follow these steps that you'll have an 1176 or an LA3-A, but the quality of sound exiting the box will be vastly improved merely by swapping out a few components... No smoke? Then the chances are that you've just made your 3630 into something resembling what it should have been in the first place." -Peter Purpose via his GroupDIY writeup
"We have a really small compressor, the Alesis 3630, which is $300. That's the main one we used on Homework and Discovery." -Daft Punk via Mix Magazine
"This upgrade of the Alesis brings the VCA section up to the same spec as a DBX 1066." -"Icarus" via Sound on Sound
Please keep in mind attempting any of the following modifications will void your warranty with Alesis.
Get a 3630
If you don't have one already, these comps can now be found for a pittance on eBay. With a little patience, you should be able to get one for less than $100.
1. Beef Up the Power Supply
Make sure you're modded unit gets plenty of current by switching to a more robust AC adapter. This wall adapter from Line6 provides a hefty 2 amps. While you're in there, consider making these component upgrades to the power section:Qty | New Component | Type | Position | Part # |
---|---|---|---|---|
2 | 220uf/35v | Capacitor | Power | C2,C3 |
2 | 2200uf/25v | Capacitor | Power | C4,C5 |
4 | UF4001 fast recovery | Diode | Power | D1,D2,D3,D4 |
2. Upgrade the VCAs and Opamps
The VCA (voltage controlled amplifier) is responsible for controlling the compressor's gain and as such has a significant effect on the its sound and performance. The THAT2180 series of VCAs represent a high-quality alternative to the stock DBX2150s. Before you remove the stock VCAs, take note of their positioning so that you are sure to install the new ones with the correct orientation. The LF347N quad opamps can be replaced with a number of chips, the LME49740, MC33079P, LT1359. Make sure that the chip you order comes in the DIP-14 format. These upgrades were originally suggested by Peter Purpose in his GroupDIY article.
Qty | New Component | Type | Position | Part # |
---|---|---|---|---|
2 | LT1359, LME49740, or MC33079P DIP-14 | Quad Opamp | Input | U2,U6 |
2 | 2180BL08-U | VCA IC | VCA | U3,U7 |
Peter Purpose's modded unit. Note that the Burr Brown Quad opamps are now unavailable and must be substituted for one of those listed above.
3. Connect the Grounds
In his article on the 3630, Peter Purpose suggests connecting all of the input and output grounds via heavy gauge copper wire.
4. Replace and/or Upgrade Passive Components
Many of the passive components, resistors and capacitors, should be improved or changed to different values. The chart below was compiled by Sound On Sound forum member "Icarus" in this post.
Qty | New Component | Type | Position | Part # |
---|---|---|---|---|
2 | 100k metal film | Resistor | Input | R12,R54 |
2 | 1.69k metal film | Resistor | Input | R14,R56 |
4 | 2.2k metal film | Resistor | Input/VCA | R13,R42,R55,R72 |
4 | 6.2k metal film | Resistor | Input/VCA | R15,R41,R57,R73 |
4 | 240k metal film | Resistor | VCA | R27,R208,R69,R211 |
4 | 20k metal film | Resistor | VCA | R22,R23,R64,R65 |
2 | 470 metal film | Resistor | VCA | R26,R68 |
2 | 100 metal film | Resistor | VCA | R29,R71 |
4 | 33 metal film | Resistor | VCA | R209,R79,R212,R102 |
2 | 5.1k metal film | Resistor | VCA | R25,R67 |
2 | 5.6k metal film | Resistor | Knee | R83,R106 |
2 | 6.8k metal film | Resistor | Knee | R17,R59 |
2 | 2.2M metal film | Resistor | Level | R10,R52 |
2 | 10k metal film | Resistor | Level | R8,R50 |
2 | 22uf audio grade electrolytic | Capacitor | Level | C11,C29 |
6 | 10uf audio grade electrolytic | Capacitor | VCA/Level/Power | C16,C43,C6,C7,C33,C55 |
2 | 22pf metal film | Capacitor | VCA | C15,C32 |
2 | 150pf silver mica | Capacitor | Input | C12,C30 |
Remove | -- | Resistor | VCA | R28,R70 |
Remove | -- | Capacitor | Level | C42,C56 |
5. Disable the Gate
If you don't find yourself using the gate function on your 3630, you can send it and its nasty artifacts packing by simply snipping the two jumpers shown in the picture.
Getting Started: 21 newbie-friendly DIY projects July 12, 2011 18:04 3 Comments
When you're first getting turned on to the world of DIY, it's easy to be tempted by projects that are beyond your abilities. Be Realistic. High voltages and hot solder are no joke and the last thing you want to do with your first project is end up with an expensive heap of broken equipment. To choose a first project that will build your skills and confidence, look for something that meets these guidelines:- Low voltages (no tubes, sorry)
- Prefabricated case and front panel
- Power supply included (pre-assembled is a plus)
- Through-hole components only (no SMD)
- Complete kit (no components to source)

Starting Small
I created the LINE2AMP reamping box and Endless Summer analog summing box kits with absolute beginners in mind. Both are completely passive and have been successfully built by numerous first-timers.
Fill Out Your 500-Series Rack
One easy way to get around the dirty business of choosing a power supply, wiring connections, and cutting holes in a case is to build modules for the API 500-series "Lunchbox" format. The 500-series modules that I recommend for beginners are:-
ClassicAPI VP25/26 or 312 Preamps
ClassicAPI's kits clone the simple API circuit with a roomy layout. This, along with good documentation and the option for pre-assembled opamps, make these the surest bet for your first 500-series project.
Difficulty: 4 -
Sound Skulptor MP573 Preamp
If you want to tackle a Neve preamp off the bat, be prepared to face a more complex circuit with little room for sloppy soldering. However, if you've got experience with a soldering iron, this full kit provides perhaps the easiest way to build a Neve-style preamp.
Difficulty: 6
Full Kits
These kits contain everything you need to complete the project, except, of course, the proper tools.
- Austin Ribbon Microphone Difficulty: 2
-
PAiA Project R
Difficulty: 2

- A12 (API-style) Difficulty: 4
- C84 ("Neutral"/Millennia-style) Difficulty: 6
- N72 (Neve-style) Difficulty: 6
- J99 (Twin Servo) Difficulty: 6
- T15 (THAT1512-based) Difficulty: 3

- Baby Animal Difficulty: 5
- 1290 Micro (Neve-style) Difficulty: 5
- Mono Portable Preamp Difficulty: 2

- MP12 (API-style) Difficulty: 4
- MP32 ("Neutral"/Discrete Opamp) Difficulty: 4
- MP66 (Tube) Difficulty: Not Recommended for Beginners (high voltage)
- MP73 (Neve-style) Difficulty: 6

- SC-1 ("Neutral"/THAT1512-based) Difficulty: 5
- X-12 Difficulty: 5

- HJFP2 (JFET) Difficulty: 5
- HVTP2 (Tube) Difficulty: Not recommended for beginners (high voltage)
Thanks for reading--I wish you the best of luck with your DIY undertakings. If you have any questions before starting your first project, feel free to ask them on the Q&A board.
5 Ways to DIY With Discrete Opamps June 17, 2011 11:09 5 Comments
This week, I was lucky enough to receive a pair of GKL255 discrete opamps in the mail from Bearcat Audio, the newest vendor on the DIY Recording Market. (Thanks guys!) Even as I opened the parcel from Montreal, my mind was already thumbing through the projects in my DIY to do/wish list for a special place to socket these new DOAs. But first, a little overview of discrete opamps for the beginner:
An operational amplifier (opamp) is a single-ended differential amplifier. This means it takes two inputs, inverted (-) and non-inverted (+), and produces a single output which is many orders of magnitude larger than the difference between the inputs. Usually opamps are manufactured as monolithic integrated circuits (ICs); however, a few intrepid designers have created their own using discrete transistors, resistors, capicitors, etc. There are three classic DOAs that most DIYers have tried to clone, imitate, or "improve": the Melcor 1731, API 2520, and Jensen 990. Each classic opamp has it's own sound which, without getting into too much audiophoolishness, can summed up thusly:- Melcor 1731 (1960's): Smooth highs and lows, beefy harmonics
- API 2520 (1970's-): Aggressive mids, solid lows, classic 70's coloration
- Jensen 990 (1980-): Low-distortion, fast transient response, wide open sound
1. Build an API or Jensen style mic preamp
The 2520 discrete opamp is at the heart of the "API Sound." And these days, there are a cornucopia of projects for the API-style preamp builder, including:
- Access 312 and Bicycle 312 are PCBs for 312-type preamps
- FiveFish X12, Seventh Circle A12, and Sound Skulptor MP12 are complete kits for building preamps in rack-mount enclosures
- Bearcat 412 a complete kit for building four 312-inspired pre's in a 1RU chassis
- ClassicAPI's VP25, VP26, 312, and 312DI are 500-series replicas of API circuits
The 990 DOA was used in several very successful preamps, including Jensen's twin servo design, which utilized two Jensen opamps and transformers. Seventh Circle Audio's J99 kit is a version of the twin servo with SCA's own 990-type opamp and Lundahl and Cinemag transformers. It's also possible to create a Jensesque preamp with JLM Audio's Baby Animal Dual kits, using any 990-type DOA and Jensen transformers.
2. Concoct your own preamp design
One of the distinct pleasures of building with discrete opamps is that they have a common footprint and can often simply be swapped. This makes the basic transformer/single opamp preamp design a great platform for experimenting with new component combinations.
- JLM's Baby Animal kits provide such a platform with a pre-fab power supply and chassis so you can focus on transformer and opamp choices.
- The Bicycle 312 Hybrid PCB is also a great place to start if you want to build your units from the ground up.
3. Build a ClassicAPI "Missing Link" Console Channel
One theory about the lack of "mojo" or "warmth" in modern recordings is that we're simply not running audio through as many transformers and gain stages as they did in the days of the large-format console. Preamps, in other words, were only part of what made those consoles sound so good. ClassicAPI provides some consolation for the console-less in the form of the VC528 ST+ console channel for the 500-series/51x Alliance. The VC528 "completes" a preamp with a fader, filters, and an output amp, running the signal through two transformers and discrete opamps of your choice along the way.
5. Make a unique hybrid 1176 compressor
Igor's 1176-style compressor for the 51x Alliance/500-series, the F76 FET, provides the option to replace the original amplifier stages with DOAs. Why not be the only engineer in town--heck in the county, heck in the tri-county area--with an "API 1176"!?
6. Upgrade the DIP8 opamps in your mixer, compressor, equalizer, converters, etc.
Until yesterday, June 16th, 2011, the sacrifice you made for using high-quality discrete opamps was not being able to use them in modern DIP8 format gear. AC Sound has begun briding this gap with a series of discrete opamps in the DIP8 format. The opamps will come in "tall" and "wide" formats and M, A, and J models (can you guess what the letters stand for?) AC Sound listed the first set of model A's on the market yesterday and plans take pre-orders the "J" and "M" models soon. Your cheap monolithic opamps had better watch their backs!
DIY Meets the API 500-series May 29, 2011 22:36
One of the most exciting trends in gear over the last few years has been the rising popularity of API's 500-series "Lunchbox" format. 500-series racks such as the Lunchbox provide an easy way to rack and power 6-11 preamps, compressors, equalizers, etc. in a single 3RU case. These racks are a boon to DIYers who want to build their own modules but don't have the skills or tools to drill and engrave their own cases.
Of course, the DIY community has found ways to have their own fun with the format. The first DIY module to the scene was Eisen Audio's DIY500 which provides a PCB and all of the hardware needed to build a transformer-balanced, opamp-based (API, Twin Servo, et al) mic preamp. Great for those who like to tinker, or if you've got some rare iron or a vintage opamp languishing in your collection. Next to come were ClassicAPI's API-style preamps for the 500-series. Created by a 70's API console owner/repairman/admirer, the VP25/VP26 and the VP312 are almost exact replicas of the original preamp circuits. ClassicAPI has also worked with Ed Anderson and Barnett Industries to clone vintage API transformers and opamps. This all makes the VPxx preamps perhaps closest thing out there to the original units--closer, in fact, than those offered by API today.
After modules had been cropping up for a couple of years, some DIYers started daydreaming about a uniquely DIY modular format. The result is 51x, a format based on the 500-series but with both +/-16v and +/-24v power rails. Last year a group of builders created the 51x Alliance 511 Rack, a DIY, 3RU, 11-space rack with an optional power supply kit. Awesome! Now we have a modular rack with a truly bulletproof power supply and enough voltage to power a real Neveish preamp, a John Hardy DOA, etc. Since the introduction of the 511 rack, the GroupDIY forum has exploded with new modules taking advantage of the higher power rails, such as Don Classics Neve clone, Igor's SSL buss compressor, and Classic API's VP312DI. And there's more to come: [silent:arts] has posted pictures of an optical compressor based on the D-AOC and Igor has announced an 1176-style FET compressor. Jeff Steiger of ClassicAPI even has plans for a 500-series/51x console (!!!) with the prototype for a "second console stage" fader and HPF/LPF module already posted. It's a great time to be alive and to DIY!
The Complete Guide to UREI/Universal Audio 1176 Revisions April 18, 2011 08:56 3 Comments
Times are good for building a DIY 1176. Where 1176's used to dangle from big-name engineers' racks like so many fruits from Tantalus' tree, they're now well within reach of anyone with a soldering iron and a modest budget. And where there was once but one DIY option (Gyraf's G1176), there are now a myriad to choose from. But why, indeed, so many projects when there is only one 1176? Revisions. According to Universal Audio's website, the 1176 underwent at least 13 revisions from 1967 to 1973. Most of these consisted of either cosmetic makeovers, such as rev H, or minor tweaks that didn't reach the audio path, such as revs D and E. Others, however, were overhauls that significantly affected the compressors' sonic character. With "Mnats" (a veritable Bill Putnam of the DIY world) now offering PCBs for revs A, D, and F/G, "which one should I build?" is becoming a common question. So without further ado, let's look at the revisions and what they can do for your sound...1176 Revison History
Revisions A/AB June 20, 1967: Wild transients tremble in fear of the enigmatic "Blue-Striped Terror."
Bill Putnam created the first 1176 compressor in 1967. Although it was the basis for all 1176 revisions, the rev A has numerous peculiarities that set it apart from the others. It is the only revision to use FETs rather than bipolar transistors in the preamp and line amps. It is also cosmetically unique, sporting a distinctive blue stripe through the meter. Finally, the rev A does not have the low-noise circuitry of later revisions, which means it imparts more harmonic distortion at the expense of a higher noise floor. The Universal Audio website tells us that there were only 25 of this revision made (serial no. #101-125), which makes them about as rare as a piece of gear can be.
Mnats' Rev A PCB is actually based on what UA calls "rev AB," which changed some resistor values and added a bypass cap for the resistor feeding the gain-reduction FET. So, for all intents and purposes it is a rev A 1176, but with a more stable and controllable limiter.
Revisions C/D/E 1970: A clean up, a suffix, and a dark new look.
Most 1176 fetishists reading this have already noticed two conspicuous differences between the rev A and the compressor most of us know today: the black front panel and the "LN" signification. These were both introduced with rev C and codified with the rev D. "LN" stands for "Low Noise," and all of the circuit changes in rev C were intended to reduce noise and distortion. These include reducing the voltage going to the gain-reduction FET to make its operation more linear, and incorporating a Q-bias pot to minimize distortion. Mnats reported that his rev D build tested 3.4dB quieter than the rev A.
Revisions C, D, and E are all in fact the same circuit with some superficial differences. For rev C, the LN circuitry was kept in its own epoxy module to protect the not-yet-patented design, but was added directly to the main PCB for rev D. Rev E merely added 220v operation in order to aggravate transients on both sides of the pond.
Universal Audio's current reproductions are based on these revisions, so if you are looking to DIY an 1176 rather than buying a new one, rev D is the way to go.
Revisions F/G 1973: Pulling out of class A / Integrating integrated circuits.
From the beginning the 1176 had used the class-A 1108 preamp for output gain. Rev F replaced this with a push-pull amplifier based on the 1109 preamp. This gives the rev F more output gain and a slightly different sonic character than previous revisions. In spite of this, this revision measures the lowest harmonic distortion of any revision, making it the best choice for those looking for 1176-style compression with less coloration.
Rev F replaced the UA-5002 output transformer with a Bournes B11148 which, according once again to the estimable Mr. Mnats, adds a small boost in the extreme high and low frequencies.
Revs F and G were also the first to incorporate integrated circuits. First, the rev F switched from a discreet to an opamp-based metering circuit, while the rev G replaced the input transformer with an NE5532 IC. This gives the rev G the potential to be the cleanest 1176 yet.
The Gyraf G1176 is based on rev F, but does not accept Ed Andersons B11148 transformer clone. Both revs F and G can be built on Mnats' rev F PCB.
Revision H The final frontier?
Silver faceplate, red "Off" button, blue UREI logo. That's it. Not much of a revision, really, and to my knowledge it has never been DIYed. Who wants to be the first to clone the front panel of the elusive revision H?
So, which one should I build?
Odds are you probably know by now which revision appeals most to you. But in case you are still trying to sort out which one is right for you, let's do a 10-second, over-simplified takeaway:Rev A: Juiciest, noisiest, vintagey-ist.
Rev D: Lower-noise, classic character. Closest to the modern repros from UA.
Rev F/G: Cleanest, unique output transformer.
Rev H: Snazzy faceplate.
All revisions use the UTC-012 input transformer, except for G, which has no input transformer.
All use the UA-5002 output transformer, except for F/G which uses the Bournes B11148.
DIY Hero: Old Thai Street Performer April 8, 2011 20:11 1 Comment
When I first visited Thailand in 2007, I was blown away by old man busking in the midst of massive street market in Chiang Mai. He plucked single notes from a squarish, wooden-fretted guitar and sang in that melismatic head voice that issues so effortlessly from Thai vocal chords. But what really made me stop to stare was that his whole setup--from the small speaker-turned-microphone he sang into to the PA system mounted on his motorized cart--appeared to be hand made. I didn't have a camera on me at the time, so I vowed to come back as soon as I could and prayed I would be able to find him again when I did. "As soon as I could" turned out to be last December (2010) and I was thrilled to find the man in the same exact spot, this time playing amplified violin. Although I felt a little like a paparazzo circling him and his contraptions taking photos, I overcame my reluctance enough to get a few good shots. So, here is my photo tribute to the incredible ingenuity and skill of a man who, for lack of a better name, I must refer to as "Old Man DIY."

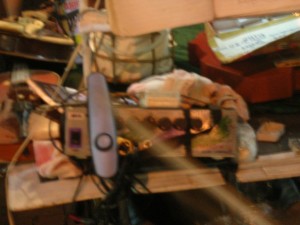
DIY Profile: Artur Fisher of DIY Audio Components March 29, 2011 12:07 1 Comment
RM-5 Assembly ManualArtur Fisher does some cool stuff with aluminum foil. Since last year, he has created a hand-made ribbon motor for DIY projects, the RE-154 and the RM-5, a microphone of his own design based on the RE-154. What makes the RM-5 really unique, besides being hand made by Artur in Latvia, is that Artur has made all of the details of its design and construction "open source" via his Designer's Diaries blog. I'm glad to have Artur as the first "DIY Profile."
What's your backround? How did you get into DIY and designing gear? I got into DIY electronics about two years later then I got into pro audio business. I started hanging around the industry when I was 17, started getting occasional payed jobs when I was 18 and got my first full-time employment when I was 19, so I am in the business for 10 years yet. My first job was in the theater as a member of stage sound crew and this was the period when I got into audio DIY. We have had a senior technician who was an engineer in electronics, so he was not just a sound guy, but was also responsible for equipment maintenance and servicing. All the electronics stuff seemed something like a black magic to me that time, but I was very curious about how is it that all these small things inside the amp do factually make sound... So I was hanging around his laboratory when he was doing some stuff and got my first basic understanding on how things work from him. After about half year I have built my first tube amp (home audio), which I still have assembled, but it wasn't what you call "designing" yet, as I have just cloned a schematic I found on the web. Then there were few attempts to make a tube guitar amp, that were marginally successful - well, they did make sound, but it wasn't exactly what I had expected, so I have understood that simple schematic cloning is not likely to work if you don't have a clear idea of what You are doing. So, I started digging old books, internet, following around people who had knowledge and skills, and after about two years after my first tube amp was built, I came to my first design - a tube guitar combo that I have calculated entirely myself from scratch, designed the chassis and made a body. It was my first small success, as some of my fellow musicians got quite excited after trying the amp, so I managed to produce and sell few pieces. I suppose that this was the moment when audio DIY culture became a major part of my life.
Why ribbon mics? Well, because they are a major trend in recording fashion right now - I just fell for ribbon mics once, but I couldn't afford to buy a Royer that time, while cheap ribbons performed way to badly to be seriously used in recording sessions. That was the moment when I asked myself a question - can't I make my own? And the long way started. Research, material sourcing and basic design works took about half-year. From the moment I had my first motor working (read, producing sound) it took another year till I brought a fully assembled good sounding microphone to my studio. I suppose that there wasn't a single session from that moment when I wouldn't use at least one of my microphones some way. In general, from a DIY point of view ribbons are very rewarding, as it is one of the rare situations when you can make something out of nothing. You can make a good condenser microphone using a pre-made chinese capsule, but nothing comes close to the feeling when you have made a working transducer out of raw materials with your own hands - and it is possible, while making your own condenser capsule is way beyond the abilities and skills of a regular DIYer, not even talking about precision machinery that You are not likely to have easily accessible in your neighborhood. There is one guy I know on the web who managed to make a condenser capsule, but from his words, it took him about 10 years to make it sound good.
Tell us about the RM-5. Is it based on anything in particular? If there is something it is based on - it is my design philosophy. I wanted to keep the microphone as simple as possible, as with all of my other designs. I wanted it to be fundamentally classical - no ribbon offsetting, no ultra-extended frequency response - pure old-school warm ribbon sound. I could easily go about 1500 - 2000 Hz up in response, but I didn't find it necessary after testing. I would rather design another model with completely different sonic signature, but I want this one to sound the way it does - conservatively charming. Advantages of modern materials provide elegant shape, compact size and quite high signal output level - these mics are absolutely usable when I just plug them into my Mackie 1640 console without any additional preamps.
On your website, you mention the RM-5 is an "open source" project. What does that mean in terms of a microphone? With "open-source" I mean that all the information about my approach to design is revealed on the site for free (and I will keep updating with more articles, when I have more time), all the materials are easily available on the web and I am open to answer any technical questions people ask me - no secrets. Feel free to make your own microphone and I will help if my advice is needed.
After you fill the current preorder for RM-5s, what's next for you and DIY Audio Components? Next - as always - is to keep working. As I can already see, there is a big interest to my pre-order offer, so I will do my best to keep providing the microphones to people who are eager for a good yet reasonably affordable ribbon sound. I have also started designing a microphone preamp. It is going to be a high-end full-tube transformer-coupled design, but I can't tell You right now when it is going to be released, hopefully by the end of the summer. Most likely it is going to be available as both - DIY kit and a ready to use assembled unit. Join the DIY Audio Components page on Facebook - all the updates are posted there. Thanks a lot to Artur Fisher of DIY Audio Components for doing this interview.
LAZ EQN (Neve 1084 500-series EQ) Available for One More Week March 5, 2011 21:40
Peter Purpose of LAZ has announced a 3rd run of his popular EQN project, a DIY Neve 1084 equalizer clone for the 500-series. But he's only taking pre-orders for one more week! If you want to get your hands on these, check out the LAZ website (www.lazpro.com) and send an email with your order to the address on the page. "Mr. Purpose" is placing his order for PCBs and components on the 12th, so make sure to get your order in by next Friday, the 11th.
Hamptone Unveils New, Low-Cost DIY Kits March 1, 2011 15:51
Scott Hampton, designer of such juicy preamps as the JFET HJFP2 and the tube HVTP2, has begun to release his long-promised low-cost kits for the Hamptone line. The new kits make the HJFP circuit available in more flexible and affordable options.- The first is the HJFP1 which adapts the HJFP mic preamp circuit to a one channel board.
- Second is the HJFA multi-purpose preamp kit. The HJFA can amplify any HI-Z signal, such as an instrument, plate reverb pickup, etc. It runs off an included wallwart, according to Hampton, is at least as quiet as the preamp power supplies.
- Finally, there's the new active HPDI that also incorporates the JFET amplifier circuit.
One New Project for Every Day in February January 31, 2011 14:29 26 Comments
DIYRecordingEquipment will turn 5 months old tomorrow, and it's come a long way since last September. So far I've compiled just over 125 DIY recording equipment projects, but I know there are a lot more out there with new ones cropping up every week. But as you may have noticed, new projects have been showing up in the directory at an embarrassingly slow rate lately. This is partially due to some new features for the site I've been working on (keep an eye out for these later this month), but I know I could be doing more to make the database more complete. That's why I've decided to add at least one new project to the directory every day next month. I decided to make this goal public so I would be sure to stick to it!DIY Ribbon Mics Hit the Front Page of WIRED January 12, 2011 22:01 1 Comment
Today the San Francisco-based technology magazine WIRED posted a photo essay about ribbon microphones and the people who love and make them. The writer, Matthew Shechmeister, covers the progression from revered vintage rarities such as the RCA 44 and Coles 4038 ribbons, to the influx of Chinese-made cheapies, to the DIY scene which (as we all know) combines quality components with a lower price tag.
In the DIY world, Shechmeister covers Rick Wilkinson who sells kits and instructions for his DIY Austin ribbon mic. The Austin ribbon kit receives some very kind words from Michael Joly of OktavaMod, who claims that a mic built from Wilkinson's plans could go up against his own Apex 205 mod, which he in turn compares to the Coles 4038.
Not everyone holds their peace, however, at the supposed union of thrift and quality provided by modded and DIY mics. John Vanderslice, producer of many awesome records, has this to say: ""There’s no bargains in audio. You have to bleed to get a good microphone. It’s going to be expensive."
While I agree with Vanderslice up to a point (how many "bargain" pieces of gear end up costing us dearly through down time and premature repairs?), I've used modded and DIY mics myself that outperform competitors far out of their price range. I suppose, however, that the time spent modding or building could count as "bleeding"--in which case I would have to agree that one doesn't get a great mic without spilling some blood. But that's the beauty of DIY: the time spent on a project isn't a cost, it's part of the reward.
You can read the full article on WIRED's website. Congrats to everyone from the DIY and recording communities who were featured!
SB-3A (DIY LA-3A) now taking pre-orders November 13, 2010 03:19 5 Comments
Last month we reported that Mike Pildis, creator of the SB4000 buss comp. project, was creating a new clone of the classic UREI LA-3A optical compressor. Pildis has now announced that he is taking pre-orders for kits and front panels.
Prices and options:
- Stereo PCB/transformer bundle, $300: contains two PCBs and 6 transformers (input, interstage, and output for each channel). Transformers are from Cinemag and Ed Anderson.
- Front panel for 2RU stereo unit, $55
- Stereo matched pair of transistors, $20
- Power transformer, $25
- Stereo component kit, $165: All of the electronic components needed to complete the build (does not include wire, VU meters, T4B optical cells)
Igor (I.J. Research) Announces Neve/Pultec Combo November 5, 2010 06:07 3 Comments
DIY's greatest overachiever is back already with a new concoction. This month, Igor has cooked up a new variation on the passive EQ theme with a Pultec-like EQ circuit and Neve-ish makeup gain. The EQ uses stepped potentiometers for recall and a stereo set can be operated in MS (mid-side) mode!
Igor estimates a stereo PCB bundle will be under $160.